How can crushers achieve energy-efficient and environmentally friendly production?
2025-03-28
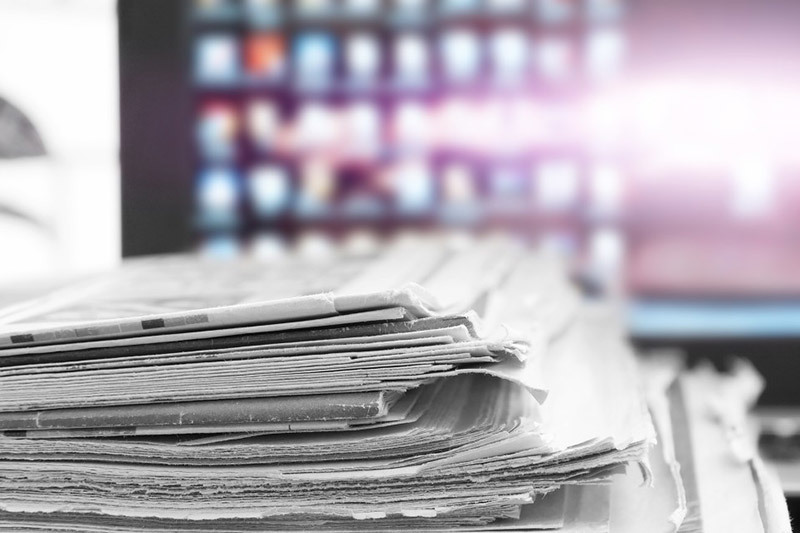
Crushers, as crucial equipment in mining, construction, and metallurgy, have energy consumption and environmental performance that directly impact the sustainability of the entire production process. With the global emphasis on energy conservation, emission reduction, and environmental protection, energy-efficient and environmentally friendly crusher production has become an inevitable trend in industry development. This article will discuss how crushers can achieve energy-efficient and environmentally friendly production from aspects such as equipment optimization, process improvement, and intelligent management.
I. Equipment Optimization
1. Research and Application of Energy-Saving Crushers
Traditional crushers have high energy consumption and low efficiency. Developing new energy-saving crushers can significantly reduce energy consumption. For example, adopting advanced crusher chamber designs, optimizing material flow paths, and reducing energy loss during the crushing process; using high-strength wear-resistant materials to extend the service life of equipment and reduce maintenance costs. In addition, new crushers can also improve energy utilization by optimizing the transmission system and reducing mechanical energy loss.
2. Application of Variable Frequency Technology
Variable frequency technology can adjust the operating speed of the crusher according to actual production needs, avoiding inefficient operation. Through variable frequency control, the crusher can maintain operation under various conditions, reducing unnecessary energy consumption. At the same time, variable frequency technology can also reduce the impact current during equipment startup, extending equipment life and reducing maintenance costs.
3. Lightweight Design
Reducing the overall weight of the crusher through lightweight design can reduce energy consumption during operation. For example, using high-strength lightweight materials to replace traditional steel, ensuring equipment strength and durability while reducing weight and energy consumption.
II. Process Improvement
1. Multi-stage Crushing Process
Traditional single-stage crushing processes often require high energy consumption, while multi-stage crushing processes can gradually reduce material particle size through graded crushing, reducing energy consumption for each crushing stage. For example, using jaw crushers for coarse crushing, followed by cone crushers or impact crushers for medium and fine crushing, can significantly reduce overall energy consumption.
2. Closed-loop System
A closed-loop system can screen the crushed materials, returning materials that do not meet the requirements to the crusher for secondary crushing, reducing repeated crushing and energy consumption. Closed-loop systems can also improve material utilization and reduce waste.
3. Dry Crushing Process
Wet crushing processes require large amounts of water and produce a large amount of wastewater, increasing environmental pressure. Dry crushing processes require no water, reducing water consumption and wastewater discharge, making them more environmentally friendly. In addition, dry crushing processes can reduce material adhesion and improve crushing efficiency.
Next: